Home | About us | Materials | Galleries | Links | Contact us
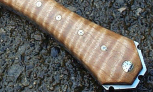
"To go well shod is half the journey".
Similarly, it is impossible to produce good work without using the best materials.
The ancients got around the vagaries of impurities in metals and (comparatively) primitive tools and techniques by making up for it with a vastly superior knowledge of the materials they were using. This shifted the balance heavily in their favour and the Japanese in particular were veritable masters of creating their swords with a truly intimate understanding of the materials they were using and how best to work with them.
Now, let's get down to cases.
I DO NOT use ivory in any shape or form, so please don't ask for it. This is a purely personal choice and is not open to negotiation, and I offer my apologies in advance if this in any way impacts on anyone visiting my site.
I offer a wide range of beautiful natural timbers for grip materials as well as Buffalo and Stag horn and jigged bone. I like hidden tangs as opposed to full/tapered tangs and my own preference is for Curly or Birds Eye Maple or Flame Birch, which I get from Norway and sometimes Russia.
Most of my knife handles feature decorative pins unless otherwise requested.
Blades for working knives are produced in a range of suitable steels, but given the choice I like to work with 01, 5160, A2 and L6 in about that order, or Sandvik 12C27 where stainless is required.
I can and will work with other alloys and I have a lot of time for steels such as D2 and ATS34, but those listed are there for a very good reason - I know them well and I know how to get the best out of them - I also know what they will do in your hand when you use the knife I make for you, and my preference is based on absolute confidence in the listed alloys.
Sheaths are typically made from wet-molded 10oz vegetable tanned leather in your choice of colour.
I make sheaths for wearing on your belt as standard, and you may customise them to be worn on one or another side, at the small of your back, angled, straight, Nordic style or whatever.
Neck sheaths are also available for smaller knives and if you have specific equipment to consider (military webbing for example) I can make to fit using Kydex.
I usually polish working knives to a satin or brushed finish and all non-stainless blades are coated with Renaissance Wax prior to delivery.
Full mirror polish is an option if you prefer it, and alternatives like sand blasted or Titanium Nitride are possible.
I can and have smelted my own metals for specific museum projects. It is hot, dirty work and very, very labour intensive. As such, I do not offer this as standard since it proves cost prohibitive in most cases, but it can be done.
Swords typically start their life as a single or multiple round bar of suitable steel and are gradually worked down to the correct size and profile. Unless you reduce a bar more than around two thirds in forging you DO NOT GET ANY BENEFIT from the process at all. The reduction is actually a form of compression during which the steel grain is fractured and made far smaller.
Grinding from bar does not allow any of this grain fracture to occur and although some of the properties of forging can be mimicked by very careful heat treating and Liquid Nitrogen soaking, forging offers very real performance benefits that cannot be obtained any other way. Most of the stock removal guys won't admit to that or discuss it, but I have proven it myself with very careful experiments and other bladesmiths have done the same.
Modern manufacturing methods provide us with an unparalelled selection of high quality metals for blades.
Coupled with the advances made in heat treatment it is possible to produce blades that can perform extremely well over a long life of use. If you mess up the heat treatment though, it all goes horribly wrong and so everything hinges on that key point.